Material Requirement Planning (MRP) adalah suatu metode manajemen yang vital dalam mengelola rantai pasokan dan produksi sebuah perusahaan.
Dengan menggunakan MRP, perusahaan dapat mengoptimalkan penggunaan sumber daya mereka, mengurangi biaya produksi, dan meningkatkan efisiensi operasional.
Lantas, apa sajakah metode dari MRP? Seperti apa contohnya? Yuk, simak selengkapnya dalam artikel berikut!
Apa itu Material Requirement Planning?
Material Requirement Planning (MRP) adalah sistem yang membantu perusahaan mengelola inventaris dan produksi mereka dengan lebih efektif.
Lebih lanjut, MRP adalah sistem yang digunakan pada industri manufaktur. Perusahaan menggunakan material requirement planning untuk mengestimasi keperluan jumlah bahan baku saat produksi dan jadwal pengiriman.
Ini melibatkan perencanaan kebutuhan bahan mentah, komponen, dan suku cadang yang diperlukan untuk memenuhi jadwal produksi.
Dengan menerapkan MRP, perusahaan dapat menghindari penumpukan inventaris yang tidak perlu, meminimalkan biaya penyimpanan, dan memastikan bahwa bahan-bahan yang diperlukan selalu tersedia tepat waktu.
Fungsi Material Requirement Planning
Material requirement planning memiliki beberapa fungsi kunci yang memainkan peran penting dalam mengelola produksi dan persediaan suatu perusahaan.
Berikut adalah beberapa fungsi utama dari material requirement planning:
1. Perencanaan Produksi
MRP memungkinkan perusahaan untuk merencanakan produksi berdasarkan permintaan pelanggan dan persediaan yang tersedia.
Dengan memiliki gambaran jelas tentang kebutuhan bahan, perusahaan dapat mengatur jadwal produksi dengan lebih akurat.
2. Manajemen Persediaan
Salah satu fungsi utama MRP adalah membantu perusahaan mengelola persediaan mereka dengan efisien. Dengan menghitung kebutuhan bersih dan mengidentifikasi kapan dan berapa banyak bahan yang diperlukan, perusahaan dapat menghindari kekurangan atau kelebihan persediaan.
3. Optimalkan Penggunaan Sumber Daya
Dengan mengetahui dengan tepat berapa banyak bahan yang diperlukan, perusahaan dapat mengoptimalkan penggunaan sumber daya mereka, termasuk tenaga kerja, mesin, dan fasilitas produksi.
4. Mengurangi Biaya Produksi
Dengan menghindari kelebihan persediaan dan mengoptimalkan penggunaan bahan-bahan, perusahaan dapat mengurangi biaya produksi secara signifikan. Ini termasuk pengurangan biaya penyimpanan, biaya pengelolaan persediaan, dan biaya produksi secara umum.
Baca Juga: Penerapan Sistem Informasi Manufaktur untuk Mengelola Bisnis
Komponen Material Requirement Planning
MRP memiliki beberapa komponen yang membantu jalannya kerja sistem. Berikut adalah beberapa komponen yang digunakan dalam MRP:
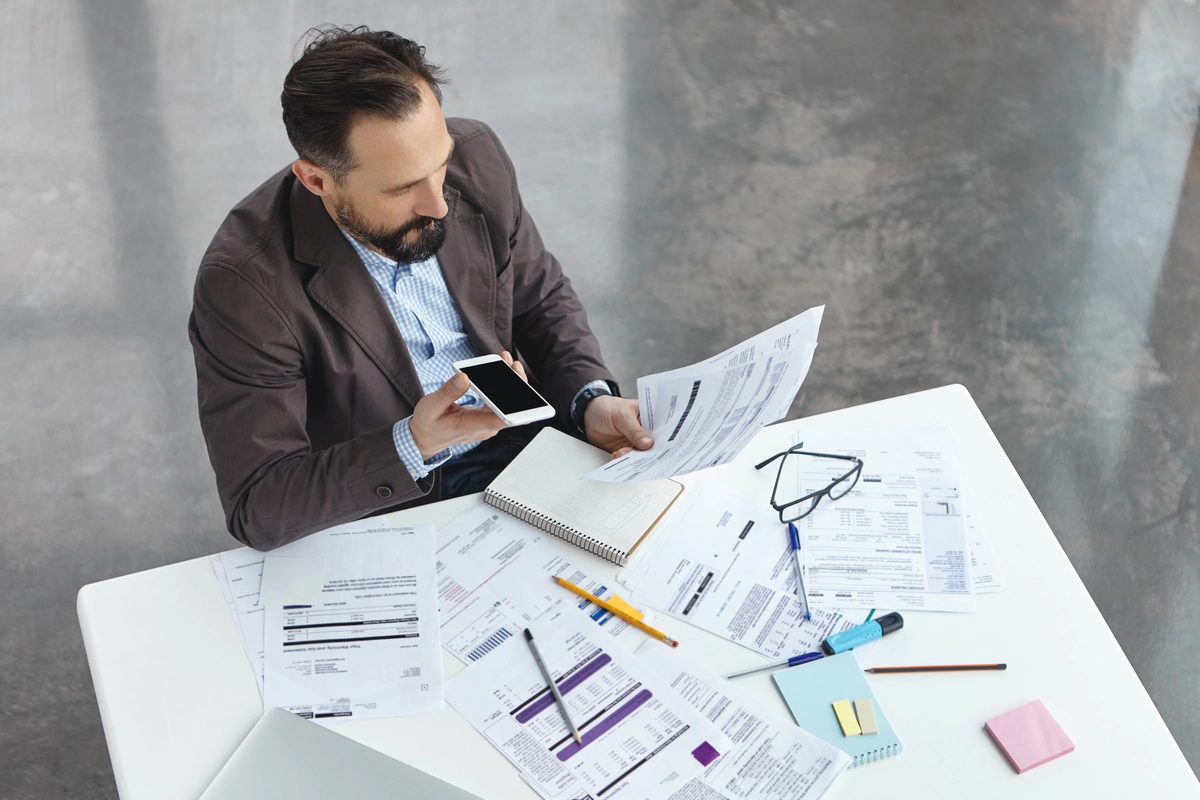
1. Bill of Materials
BOM adalah daftar lengkap semua komponen, sub-assembly, dan bahan mentah yang diperlukan untuk memproduksi suatu produk. Ini berfungsi sebagai dasar proses MRP
2. Master Production Schedule (MPS)
MPS adalah rencana rinci yang menguraikan jadwal produksi untuk periode tertentu, biasanya mencakup beberapa minggu atau bulan. Ini memperhitungkan permintaan pelanggan, inventaris yang tersedia, dan kapasitas produksi.
3. Catatan Status Inventaris
Catatan ini memberikan informasi real time tentang jumlah setiap item yang ada dalam stok. Data ini sangat penting untuk menghitung kebutuhan bersih.
4. Surat Pesanan Pembelian
Surat pesanan dibuat berdasarkan kebutuhan yang diuraikan dalam MRP. Surat pesanan ini dikirimkan kepada pemasok untuk memastikan pasokan bahan tepat waktu.
5. Perencanaan Kapasitas
Perencanaan kapasitas melibatkan penilaian kapasitas produksi perusahaan untuk memastikan selaras dengan jadwal produksi yang diuraikan dalam MPS.
Cara Kerja MRP
Perangkat lunak MRP (Material Requirement Planning) mengumpulkan data dari Bill of Materials, yaitu daftar semua bahan baku, subassemblies, dan komponen penting lainnya yang diperlukan untuk memproduksi suatu barang, lengkap dengan jumlah yang dibutuhkan.
Selain itu, perangkat lunak MRP juga memanfaatkan informasi inventaris dan jadwal produksi utama untuk menghitung kebutuhan bahan baku serta waktu pemanfaatan bahan baku tersebut selama proses produksi berlangsung.
Metode ini sangat efektif untuk berbagai jenis perusahaan manufaktur, termasuk manufaktur diskrit (seperti pabrik mobil, alat perkakas, dan sejenisnya) dan manufaktur proses (misalnya pabrik makanan dan minuman, pabrik kimia, dan lainnya).
Hal ini menjadi alasan mengapa banyak perusahaan manufaktur di seluruh dunia menerapkan metode ini. Pada awalnya, perencanaan kebutuhan material menggunakan komputer mainframe untuk mengelola informasi dari Bill of Materials untuk produk tertentu, yang kemudian diubah menjadi rencana pembelian dan rencana produksi.
Beberapa tahun kemudian, perangkat lunak MRP menambahkan fitur umpan balik yang memudahkan manajer produksi untuk melakukan perubahan atau pembaruan langsung ke dalam sistem.
Seiring berjalannya waktu, sistem perencanaan kebutuhan material terus berkembang dan kini dapat terintegrasi dengan bidang pemasaran, keuangan, hingga sumber daya manusia dalam proses perencanaan produksi. Karena kompleksitasnya, perencanaan kebutuhan material pada tahap ini sering disebut sebagai MRP II.
Metode MRP (Material Requirement Planning)
MRP adalah sistem yang bekerja dengan mengidentifikasi kebutuhan bahan mentah, komponen, dan suku cadang yang diperlukan untuk memenuhi jadwal produksi.
Berikut adalah metode MRP Material Requirement Planning yang umum diterapkan:
1. Identifikasi Kebutuhan
Pertama, perusahaan harus mengidentifikasi semua bahan mentah, komponen, dan suku cadang yang diperlukan untuk memproduksi barang jadi. Ini termasuk segala hal mulai dari bahan mentah dasar hingga komponen lebih kompleks.
2. Perhitungan Kebutuhan Bersih
Dengan menggunakan BOM dan MPS, MRP menghitung kebutuhan bersih untuk setiap komponen. Ini dilakukan dengan mengurangi persediaan saat ini dari total kebutuhan.
3. Pemesanan Bahan
Setelah kebutuhan bersih dihitung, MRP akan menghasilkan daftar pesanan pembelian untuk bahan-bahan yang diperlukan. Pesanan ini dikirim ke pemasok untuk memastikan pasokan tepat waktu.
4. Pemantauan Persediaan
Proses MRP membutuhkan pemantauan dan penyesuaian terus-menerus. Perusahaan perlu memantau status persediaan dan memperbarui rencana produksi jika ada perubahan dalam permintaan atau pasokan.
5. Evaluasi dan Perbaikan
Setelah implementasi, penting untuk mengevaluasi kinerja MRP secara teratur dan melakukan perbaikan jika diperlukan. Hal ini termasuk memastikan bahwa data yang dimasukkan akurat dan bahwa perangkat lunak MRP bekerja secara optimal.
Baca juga: Property Management System: Pengertian, Manfaat, Jenis, dan Aplikasinya
Perbedaan MRP dan ERP
MRP dan ERP adalah singkatan yang memiliki pengucapan serupa dan keduanya digunakan dalam industri manufaktur. Namun, terdapat beberapa perbedaan penting antara kedua sistem ini.
Perbedaan paling mencolok antara MRP dan ERP adalah bahwa MRP merupakan perangkat lunak yang berdiri sendiri dengan fokus pada modul dan fitur manufaktur, sedangkan ERP memiliki kemampuan untuk terintegrasi dengan perangkat lunak lain seperti HR (Human Resources), POS (Point of Sales), dan lainnya.
Karena ERP dapat dimanfaatkan oleh berbagai departemen dan memiliki alur kerja yang lebih kompleks, sistem ini sangat cocok untuk bisnis yang sudah mencapai ukuran menengah hingga besar. Secara umum, ERP mampu mendukung berbagai jenis industri, bukan hanya sektor manufaktur.
Tahapan Material Requirement Planning
Berikut adalah empat tahap dasar dalam MRP yang harus diperhatikan.
1. Membuat Perkiraan dan Kebutuhan Bahan
Tahap pertama dalam implementasi sistem MRP adalah mengidentifikasi permintaan pelanggan. Dengan cara ini, perusahaan dapat menganalisis kebutuhan atau hal-hal yang diperlukan untuk memenuhi permintaan tersebut.
Pada tahap ini, sistem MRP akan membagi permintaan menjadi dua kategori: bahan baku dan komponen tertentu. Dengan menggunakan fitur bill of material, perusahaan dapat mengakses daftar bahan mentah, rakitan, dan komponen yang diperlukan.
2. Membandingkan Permintaan dengan Persediaan dan Mengalokasikan Sumber Daya
Setelah melakukan perkiraan permintaan dan menerima masukan dari konsumen, daftar permintaan akan dibandingkan dengan persediaan yang ada. Selanjutnya, inventaris yang sudah ada akan didistribusikan ke titik-titik persediaan. Dengan demikian, perangkat lunak MRP dapat mengatur alokasi sumber daya perusahaan secara efektif.
3. Penjadwalan Produksi
Tahap penting lainnya dalam penerapan sistem MRP adalah menghitung jumlah waktu dan tenaga yang dibutuhkan untuk menyelesaikan proses manufaktur. Biasanya, perusahaan menetapkan batas waktu agar produksi dapat diselesaikan sesuai dengan permintaan konsumen.
Setelah bahan mentah diolah menjadi produk, masih ada tahapan pengiriman sebelum produk sampai kepada konsumen. Oleh karena itu, ketepatan waktu dalam produksi adalah faktor yang sangat penting dalam proses ini.
4. Pemantauan Proses Produksi
Kualitas produk menjadi prioritas utama bagi perusahaan. Oleh karena itu, pemantauan terhadap proses produksi sangat penting untuk mendeteksi kemungkinan-kemungkinan yang tidak sesuai harapan.
Tujuannya adalah untuk meningkatkan kualitas produk. Perangkat lunak MRP tidak hanya dapat memberi peringatan kepada manajer secara otomatis jika ada proses yang tidak memenuhi standar, tetapi juga dapat memberikan rekomendasi untuk merencanakan penyelesaian sesuai dengan tenggat waktu produksi.
Contoh Material Requirement Planning
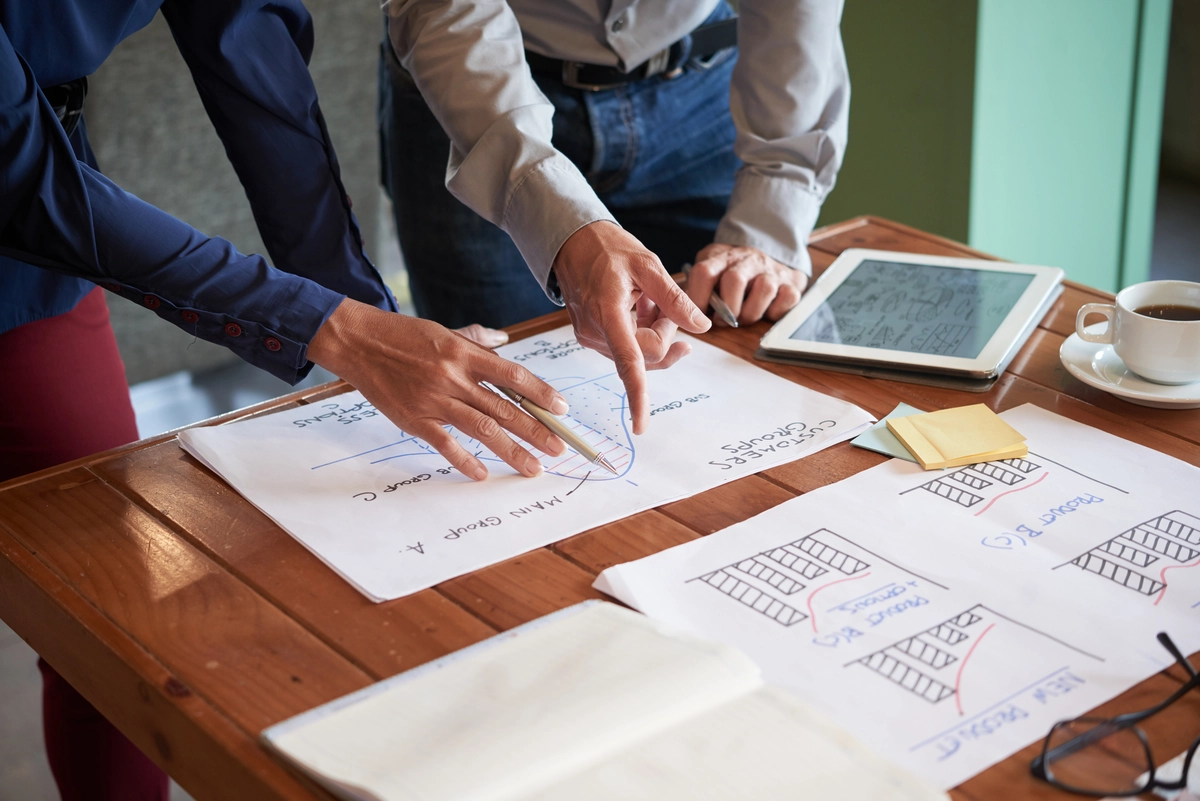
Mari kita lihat contoh material requirement planning dalam sebuah perusahaan manufaktur sepatu di Indonesia, yaitu perusahaan sepatu Maju Jaya.
Perusahaan sepatu Maju Jaya adalah produsen sepatu terkemuka di Indonesia. Perusahaan menghasilkan berbagai jenis sepatu, termasuk sepatu olahraga, sepatu formal, dan sandal.
1. Identifikasi Bahan-Bahan Utama
- Kulit sintetis dan kulit asli
- Sol karet
- Kain lapis dalam
- Benang dan perekat
2. MPS dan BOM
- Master Production Schedule (MPS) mereka menentukan bahwa untuk bulan ini, mereka harus memproduksi 10.000 pasang sepatu olahraga.
- Bill of Materials (BOM) untuk sepatu olahraga mencakup: 1 pasang kulit sintetis, 1 sol karet, 0,5 meter kain lapis dalam, 10 meter benang, dan perekat secukupnya.
3. Pengumpulan Data
Data diambil dari inventaris saat ini:
- 2.000 pasang kulit sintetis
- 3.000 sol karet
- 500 meter kain lapis dalam
- 15.000 meter benang dan perekat yang mencukupi.
4. Perhitungan Kebutuhan Bersih
Misalkan, untuk memproduksi 10.000 pasang sepatu olahraga, mereka membutuhkan 10.000 pasang kulit sintetis, 10.000 sol karet, 5.000 meter kain lapis dalam, 100.000 meter benang, dan perekat sesuai kebutuhan.
5. Penjadwalan Produksi
Berdasarkan kebutuhan bersih dan kapasitas produksi mereka, Maju Jaya menjadwalkan produksi sepatu olahraga selama bulan ini.
6. Pemesanan Bahan
MRP menghasilkan daftar pesanan pembelian, termasuk:
- 8.000 pasang kulit sintetis
- 7.000 sol karet
- 4.500 meter kain lapis dalam
- 90.000 meter benang
- Perekat sesuai kebutuhan
7. Pemantauan dan Penyesuaian
Tim produksi dan manajer persediaan terus memantau tingkat inventaris dan kemajuan produksi sepanjang bulan. Jika terjadi perubahan dalam permintaan atau pasokan, mereka menyesuaikan jadwal produksi dan pesanan bahan.
8. Evaluasi Kerja
Akhir bulan, Maju Jaya mengevaluasi kinerja MRP. Mereka menilai apakah produksi berjalan sesuai rencana, apakah persediaan bahan terjaga dengan baik, dan apakah biaya produksi terkendali.
Baca Juga: Mengenal Pengertian, Tujuan, Jenis Hingga Aplikasi Proses Manufaktur
Itulah dia ulasan lengkap mengenai material requirement planning. Pada intinya, MRP adalah suatu metode untuk merencanakan serta mengelola produksi dan persediaan suatu perusahaan.
Dengan menerapkan MRP dengan baik, perusahaan dapat mengoptimalkan produksi mereka, mengurangi biaya, dan meningkatkan efisiensi operasional secara signifikan.
Jadi, dapat disimpulkan bahwa material requirement planning (MRP) adalah contoh perencanaan yang penting dalam dunia bisnis.
Berbicara tentang perencanaan dalam dunia bisnis, kita tidak bisa mengabaikan pentingnya perencanaan yang tepat dalam pengembangan situs web atau aplikasi.
Pasalnya, sebuah situs web dan aplikasi yang sukses memerlukan perencanaan matang, desain menarik, dan implementasi yang cermat.
Nah, jika Anda membutuhkan jasa pembuatan website atau aplikasi untuk kebutuhan bisnis, Sekawan Media dapat menjadi solusinya!
Sekawan Media menawarkan solusi di bidang pembuatan website dan aplikasi yang bisa digunakan untuk kebutuhan perusahaan Anda.
Apabila Anda membutuhkan informasi lebih lanjut, jangan ragu untuk mengunjungi situs web Sekawan Media sekarang juga, ya!